This guide will explain what is bottleneck and how to deal with it in managing your operations.
What is Bottleneck?
A bottleneck is a phenomenon where overcrowding occurs in a manufacturing process. For example, a line in an assembly or networking in a system gets overwhelmed with products on the production line and it can’t be processed at the same time. Bottlenecks are a byproduct of business. You are not supposed to get frustrated by them because these issues can be rectified in the due course of time.
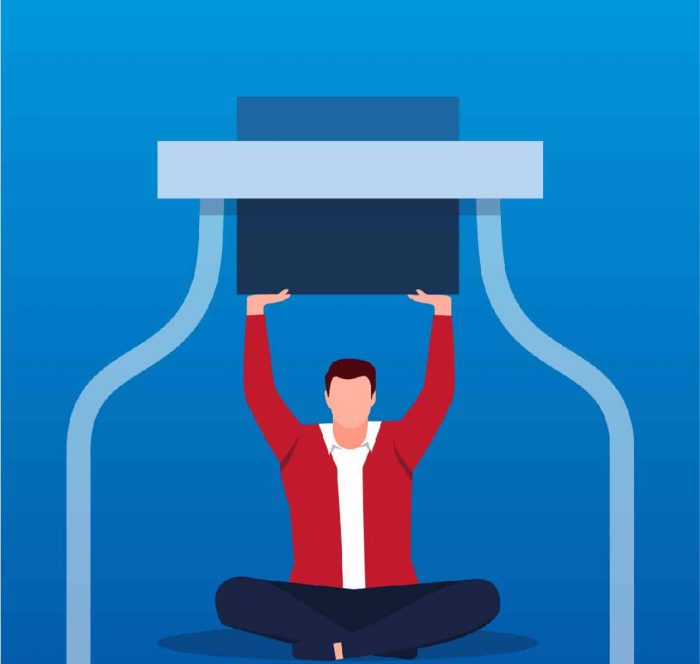
On that note, bottlenecks happen when there are too much caseload and burden on a key processing plant, or a significant area that’s held responsible for delegating things. A common real-life example of a bottleneck could be traffic jams. They occur when the traffic signals are not working, when there’s an emergency situation or a traffic police warden is deployed at the area in case of traffic lights’ malfunctioning.
These kinds of irregularities cause the process to slow down and it further causes a deadlock or delay. Not to mention the fact that the cost to repair damages and time spent is something that many organizations cannot afford. This is why it is important to deal with bottlenecks before they happen. Here’s how you can do it. Read more…
Don’t Worry About Deluge:
In general terms, deluge means, ‘a severe flood’. This flood could be anything; think about overproduction when it is clearly not needed. Think about delivering more products, or over-processing beyond the capacity of the plant and/or facility in question.
Operation managers are responsible for accounting for balancing things. They enforce certain policies to work a few measures that ensure the check n’ balance between products and production. Apply the same formula to any other process to get by with a smooth experience.
What If Deluge Is Imminent?
In that case, I’d surmise that you need to grow the “procedure volume”. A lot of manufacturing plants have a certain quota that they need to meet regardless of the demand curve. Such businesses have good hindsight that helps them to clear their stock by the end of the fiscal year.
But then again, all businesses are not alike. There are times when overproduction can occur – and in that case, you need to prevent it before that happens. The best course of action would be to increase the production volume, or the ability of the plant to simultaneously deal with the capacity to work.
One good recommendation to help deal with the aforementioned predicament is appended below:
Valuable Addition of Assets:
Adding resources for the bottleneck procedure serves the purpose. By adding the strength of the assets which are getting the job done through an operation we can get desired results; given the condition that the upper count should not be included in this. In other words, add resources without worrying about the ceiling factor as part of sustaining the project’s speed and recovery on a priority basis.
How to deal with bottlenecks in operations management?
1. Bottleneck Should Always Have a Significant Role:
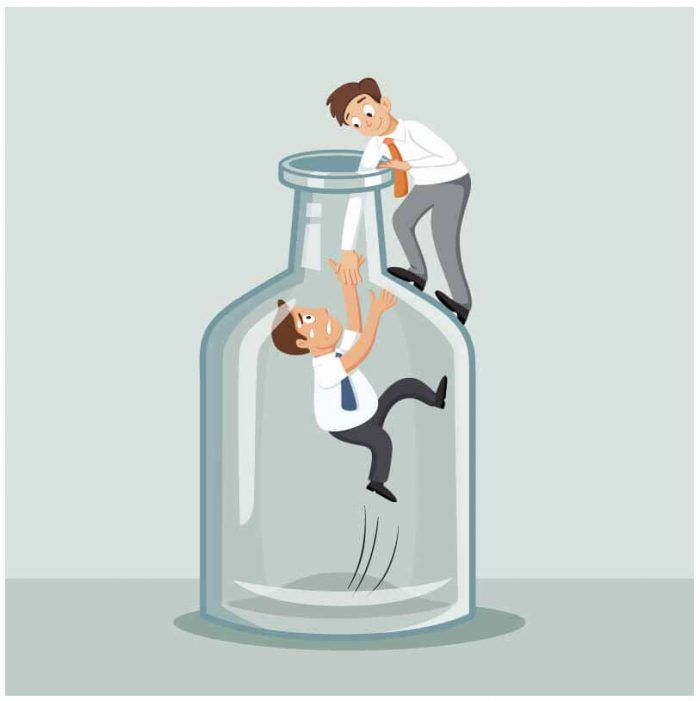
Okay, a bottleneck has come up. Don’t panic. What’s the worse that could happen? Well, a lot of things can go downhill, but if you are willing to carefully mitigate the damage, you may as well come out happy on the other side.
To minimize the bottleneck’s effect/ damages, you can start by monitoring everything. See what went wrong at the labors’ side; what happened during the production phase?; is everything okay at the packaging side etc.?
Monitoring always tends to solve a part of the bottleneck issues because it helps to identify the problem – or a number of problems for that matter.
2. Bottleneck Solutions Should Work Qualitatively not Quantitatively:
Instead of mass mitigation, try to focus on fixing one bottleneck issue at a time. By focusing on quality-oriented results, you are ensuring that these issues will not pop up anytime soon.
3. Inspect The Manufacturer Program:
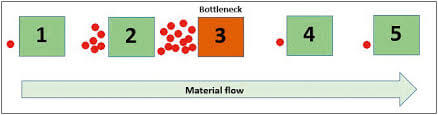
Source: De Gruyter
You must inspect each process at a minute level, given that you are part of a plant that’s responsible for manufacturing something. Fortunately, manufacturing plant bottleneck issues don’t come up that often because the technology has advanced a lot these days.
However, there is always a chance of things going awry. Keep a backup plan on the side for worst-case scenario situations – especially when you are actively working in an environment where production is one of the main cogs of the business wheels.
4. Grow Operational Work Span:
Bottleneck mitigation is inversely proportioned to functional work activities. To minimize the possibility of a bottleneck occurring again, why don’t you try and grow the operation work span? If you have enough monetary resources, perhaps it is a good idea to expand the ability to multitask and execute different activities simultaneously.
5. Reduce Break Times:
Don’t take too much or useless breaks during an ongoing process as it adversely affects the whole operation. What if the crew is on an unscheduled break at the time of a bottleneck incident? Of course, there will be repercussions for that, but the unforeseen damage could have been avoided easily if everyone responsible was available at that time.
On a side note, also try your level best to minimize the changeover time which means switching from one process to another during simultaneous activities.
6. Bottleneck’s Assets’ Performance should be Improved:
Formulize a procedure with proper processing and systemized methodology so that there will be fewer chances of an error to occur.
For things to get started, you need to gather resources to meet the requirements and then come up with essential documentation to highlight different steps for the aforementioned processes. You can, then, forward that documentation to the operation manager or people higher up the food chain to help implement a proper system where everything can work according to the grand plan.
7. Strategic Realignment & Division of Bottleneck’s Work:
Breakdown complex parts of a bottleneck operation into simpler or relatively small portions so that any number of countermeasures to mitigate the problems can be performed easily. Keep your strategic realignment strategy short, clear and concise so that those people who are concerned with the implementation of that strategy, they can follow the direction without the possibility of further messing up things.
Conclusion:
Let’s end it with a famous phrase: ‘Every challenge is a new opportunity.’ Obviously, during the course of your career, there will be pitfalls and obstacles that will set you back by a couple of miles. Adversity is part of the game. Therefore, don’t let it tug you down. Bottlenecks are a naturally occurring consequence of any ongoing process.
The only thing that matters is how you recover from such incidents. Of course, with the help of the aforementioned tips, you can minimize the possibility of any number of bottlenecks from happening again. If you liked this write-up or felt that we missed something, feel free to use the comments section below. We would love to hear your thoughts on this critical issue.